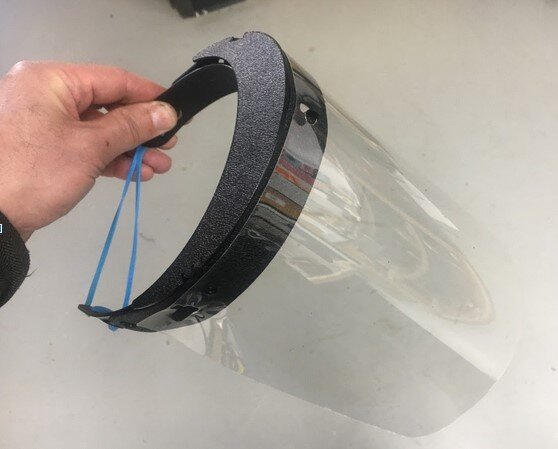
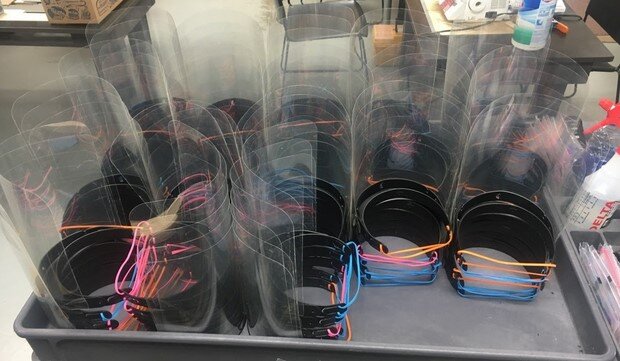

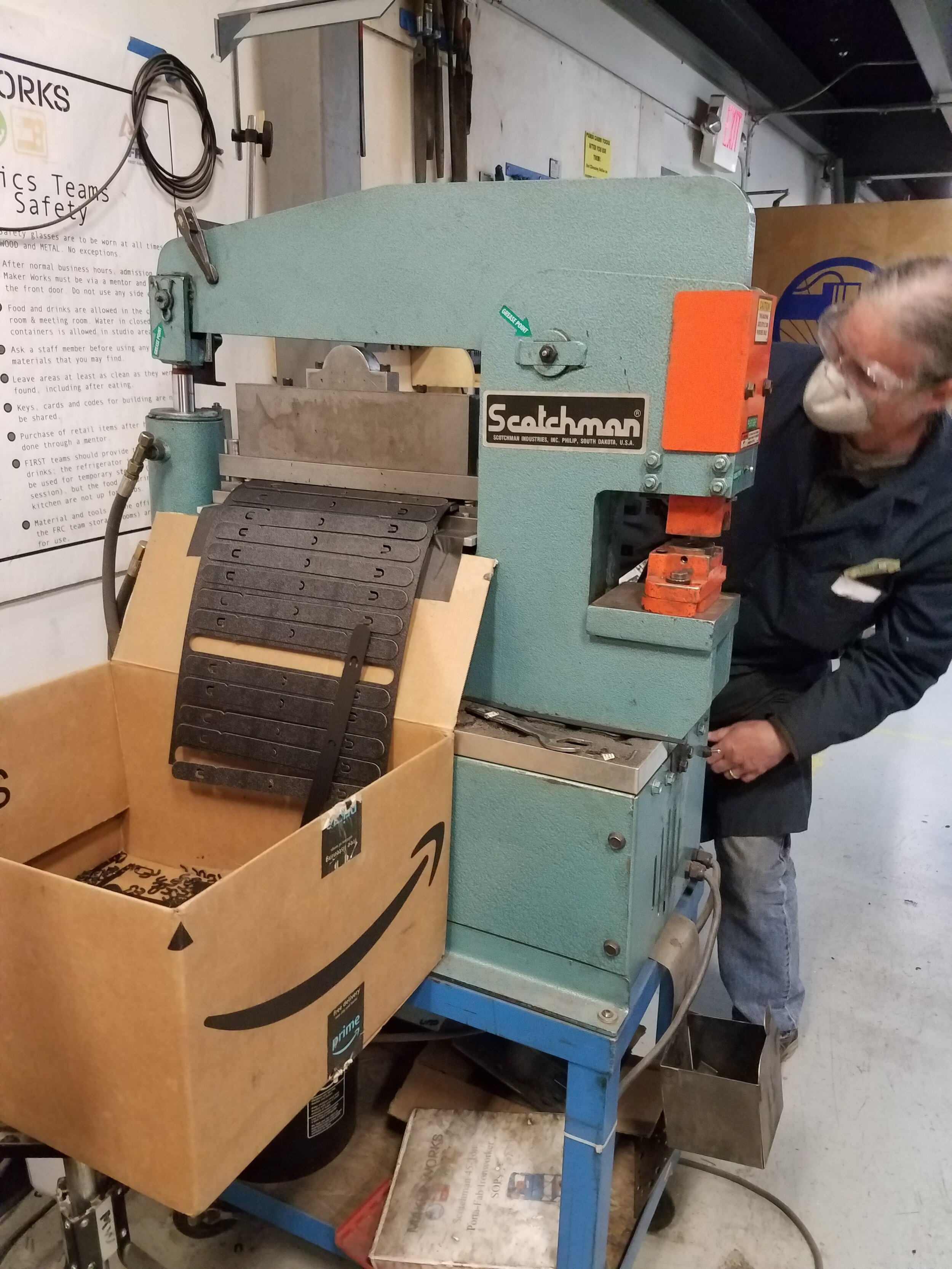
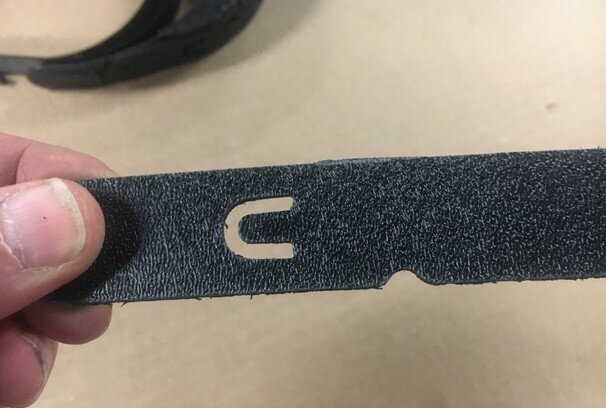
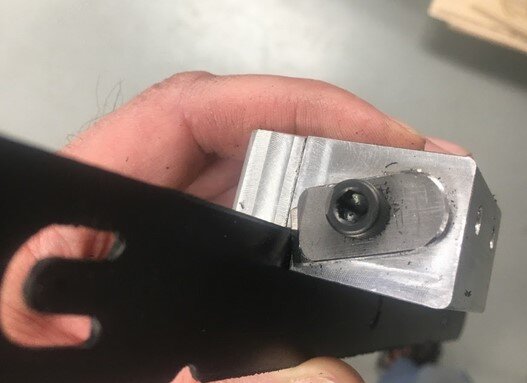
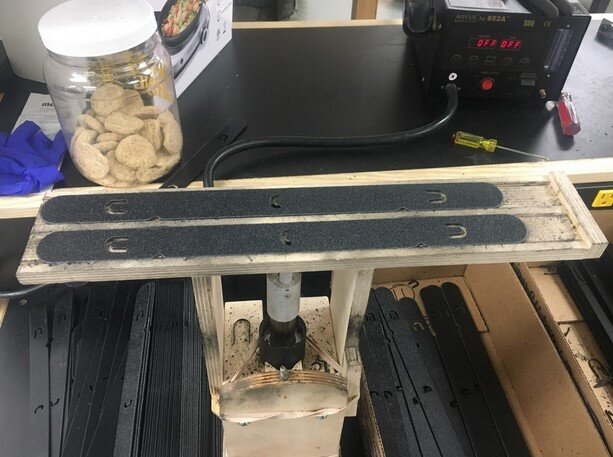
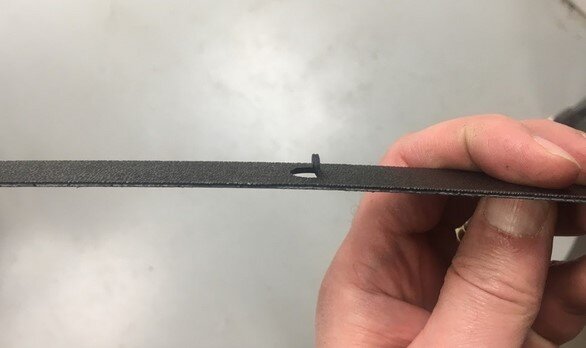
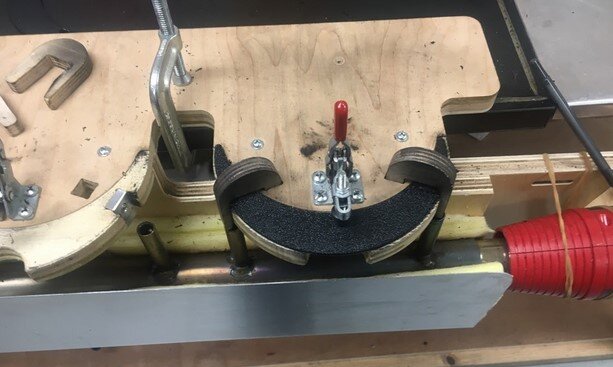
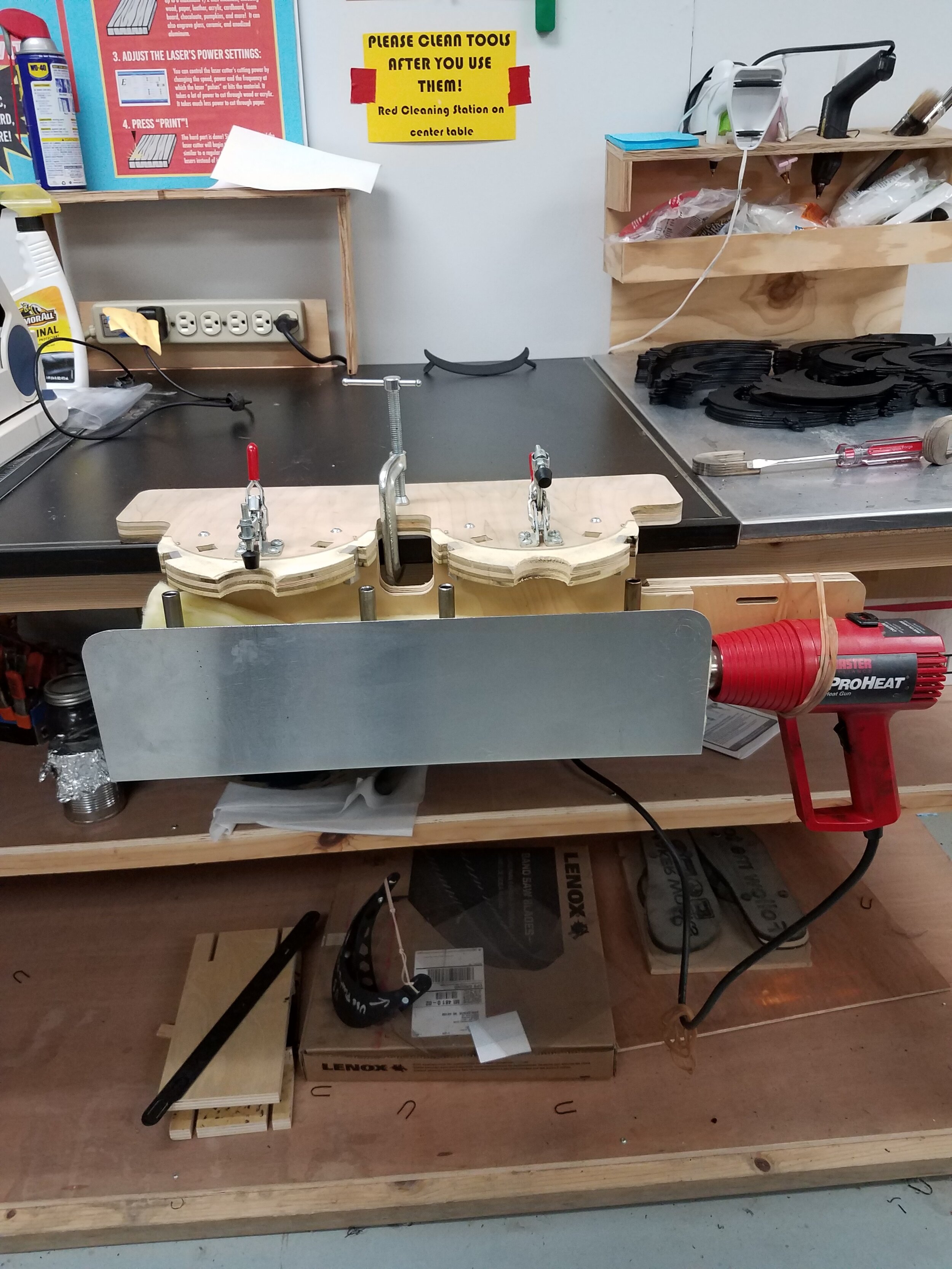
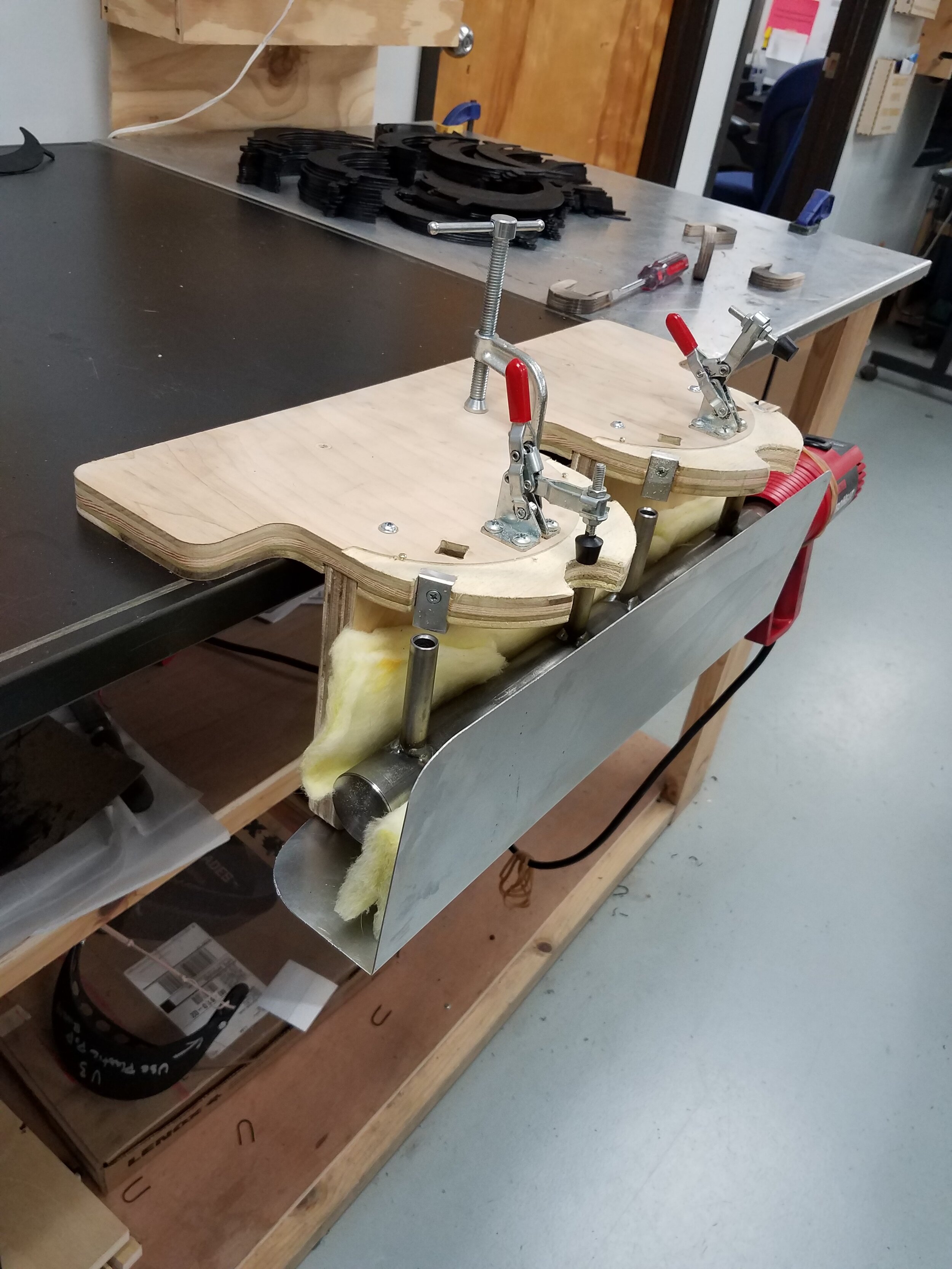
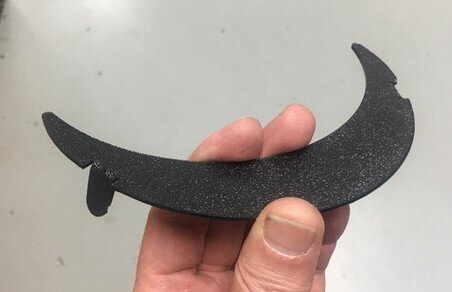


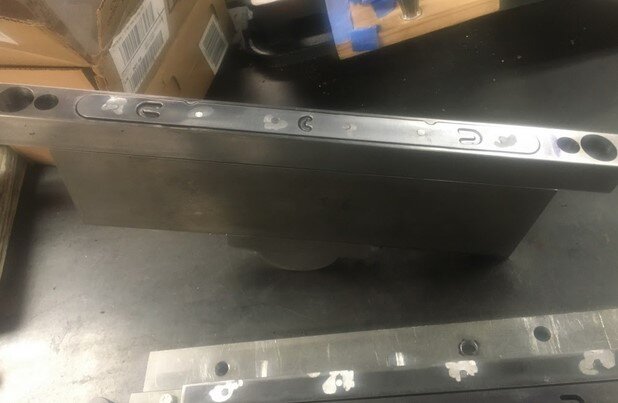
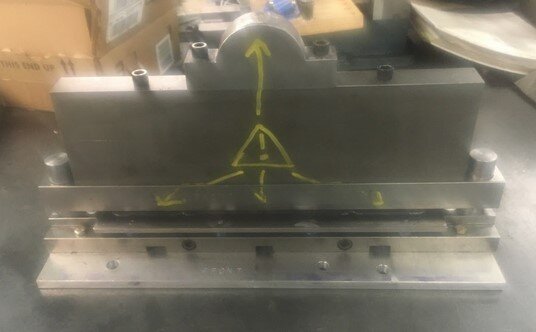
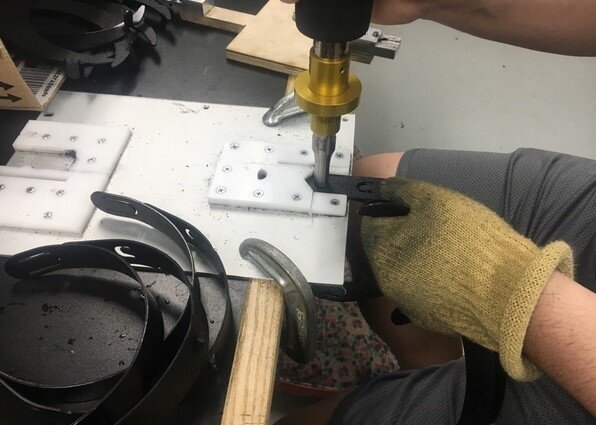
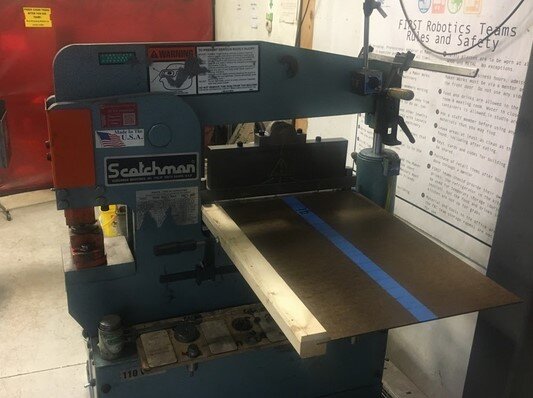
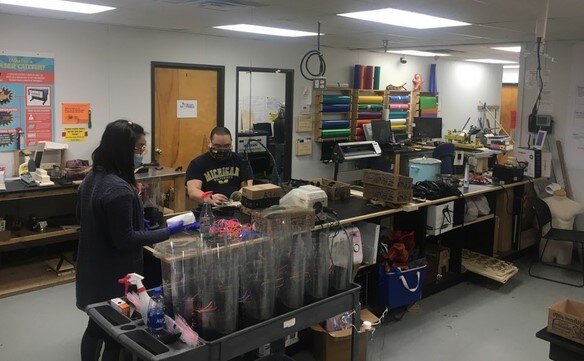
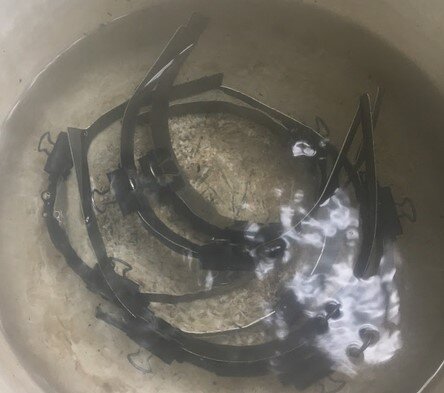
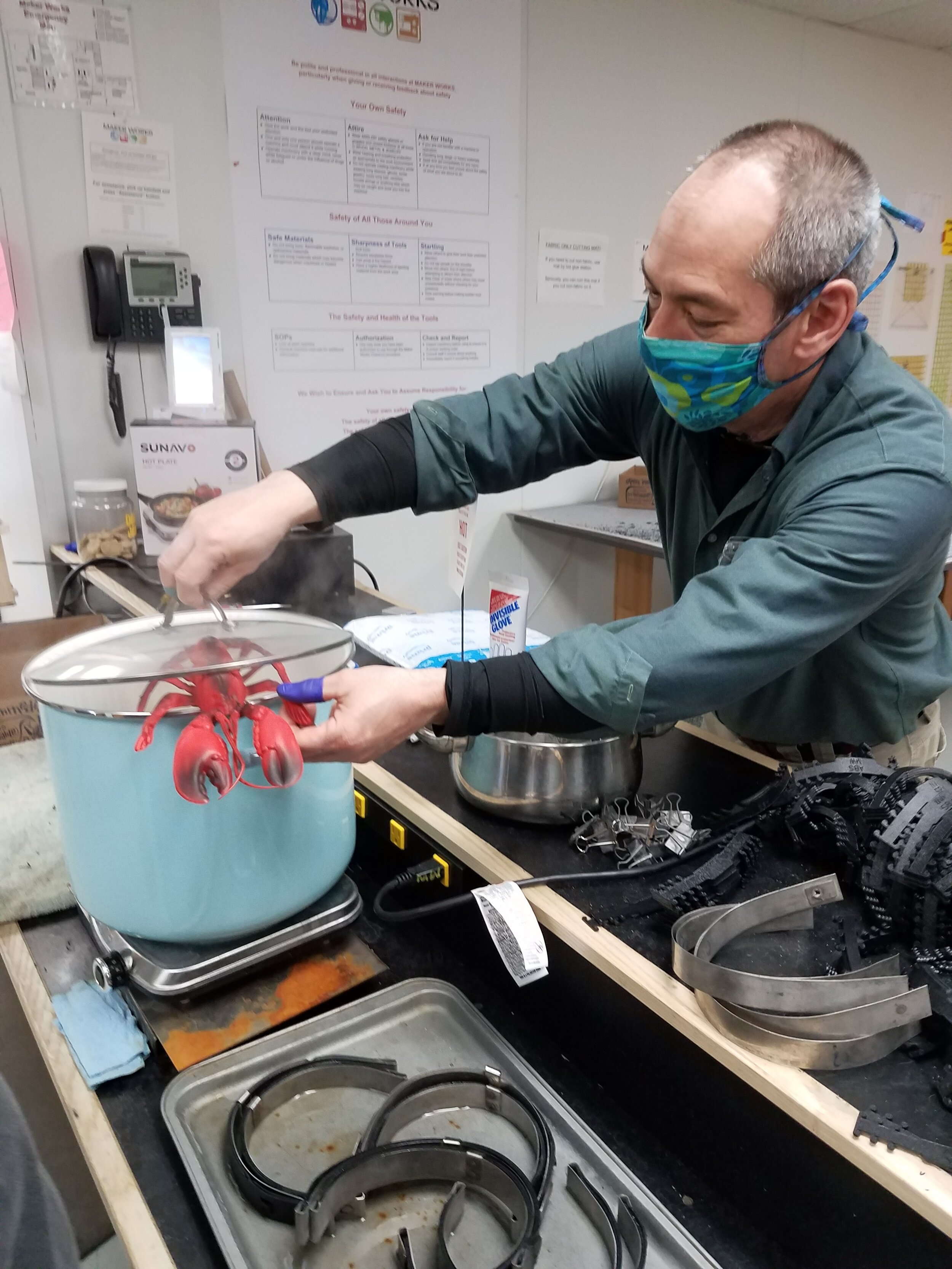
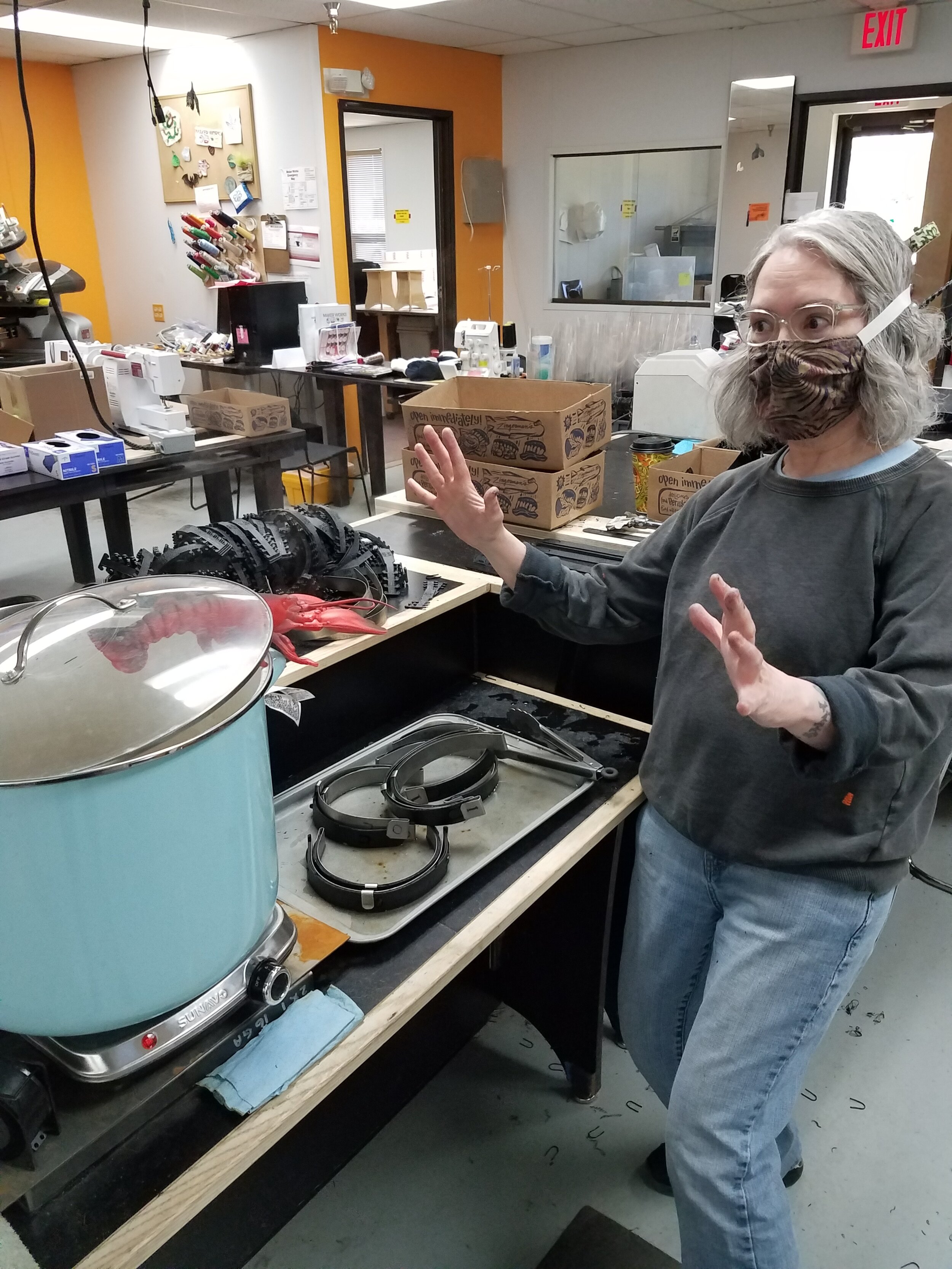
Almost from the start of the COVID-19 pandemic here in Michigan, staff and members were thinking about how to use their making skills to help hospitals and other health care providers meet the need, especially around personal protective equipment like masks and face shields.
The Ann Arbor Sewing Center and others in the community jumped in to fabric face mask production, and many thousands were produced (and are still being produced, now that everyone is being asked to wear them). And early on, people were 3D printing a succession of designs for face shields. But Maker Works only had two fused-filament printers, and our two resin printers are much slower (though very high resolution), and it takes 30 minutes on up to print even the most optimized design. We wanted to produce a higher volume, since it seemed like there was great need locally and regionally. Irene agreed to lead the charge.
Looking at the design for the popular 3D face shield holder from Prusa and others, it looked like two curved flat bands.
Example of 3D Printed Headband
Stagehands have a saying—Never lift what you can drag, never drag what you can roll, never roll what you can leave.
When looking at a plastic object, we might offer—Don't machine what you can 3D print, don't 3D print what you can cast, don't cast what you can injection mold, don't injection mold what you can laser cut from flat, and don't laser cut what you can punch. (All these suppose you have the volumes, time, and capital to invest in the various technologies.) In this case, the two bands suggest the possibility that we could create a similar face shield holder much faster by making two flat bands and bonding them together. Tabs can be used to secure the face shield and also as a connection point for the rubber band at the rear, so the stock can be flat.
We initially laser cut two strips from 1/16th inch ABS plastic sheet (we had some in the shop from some vacuum forming) and bonded them with acetone, but the bands did not bend uniformly due to the cut outs for the tabs. ABS happens to relax at just over 200°F, so we made stainless steel forms in a C shape, clipped bands to them, and boiled them in water for 2 minutes. The bands then assumed the correct shape. It did seem strange to have a boiling pot of water as part of our production line, though. Marty has since provided a mascot, Louie the Lobster, for this part of the process.
Bonding with acetone took a while per joint and we had trouble with some joints even with clamping (probably due to the raised edge the laser can leave). It's also messy and there are fumes. Bob Gifford, Automotive Sales Manager of Branson Ultrasonics in Sterling Heights, MI, very kindly tested, set up, and loaned us an ultrasonic welder for bonding the two straps together, a huge improvement in time and robustness. (It is one of the more fun jobs on the line.)
For some weeks, we expected to run out of the clear plastic for the shields themselves at any moment, but Operation Face Shield, MW members, U of M, and others always came up with material that we could machine on the ShopBot or cut on the laser. More recently, Mike Wright of Flint's makerspace Factory Two arranged a group purchase of some PET film they found in Chicago, and a local company Sensitile generously has been cutting shields out of this material for us. We also received generous donations of ABS plastic and clear plastic from the U of M Hospital, and support from EMU's Engage. AHA! (All Hands Active) makerspace helped laser cut a lot of shields for us and MS2 (Midwestern Software Solutions) provided thousands of rubber bands.
(As an alternative to laser cutting, we did get some steel rule die cutting blades, but have not experimented with them. Hopefully we won't have a need associated with PPE to revisit that.)
A later improvement was the addition of a visor element that almost entirely covers the space between the shield and the user's forehead, which was a concern for some users. This required a third laser-cut piece and heat bending the two tabs.
For some weeks then, our production was:
laser cutting outer band, inner bands, and visor (about 40-50 seconds per item)
hot air rework station used to selectively heat and bend the center tab out
2 minute boiling water bath to take the shape
two ultrasonic welds to secure two bands to each other
two more welds to secure visor to outer band
install shield
install rubber band
sanitize (in an ozone closet, provided by Nicholas Cucinelli of U of M's COVID response team)
Each day 3-5 Maker Works staff, wearing masks and socially distancing, would volunteer their time to produce several hundred face shields.
Our limiting factor was the laser cutting. Even with two lasers cutting full time, none of the other operations took longer than the cutting. So we looked at how to speed up the production of the bands.
The answer turned out to be a custom compound punching die. (A compound punching die both punched out elements (in our case, the areas around tabs) and also "blanks" the object, cutting the band from the surrounding material. This means the dies parts are much more complicated—there are two separate stripper plates (to push the cut object back level with the top of the die) each with their own die bolts and powerful die springs. But, it accomplishes both the punching and the blanking in one quick operation, which is what we wanted for the production rate.) Using design information from https://www.misumi-techcentral.com/tt/en/press/die-design/, 1045 medium-carbon steel from Alro in Jackson (our local Alro is closed at the moment), hardware from McMaster-Carr, and tooling from MSC Industrial, we used Fusion 360 CAD and CAM, and the Tormach CNC mill and Clausing lathe to design and machine the following:
punching die (upper and lower parts)
base plate (aluminum)
spacer (mild steel)
stripper plates (upper and lower)
tapered alignment pins (1" steel rods)
We installed these on the Scotchman 45-ton ironworker in place of the general purpose shear, then Al built an infeed table.
Cycle time for a single band dropped to around 10 seconds, and quality and consistency was very good. We did need to deburr one side, so we created a custom deburring tool using a tiny piece of a utility blade clamped in an aluminum holder.
Fortunately for everyone, within a day of the punch going into production mode, we received word from the last local hospital that their need for face shields was satisfied for the moment. We've been asked to go into standby mode, so as we're writing this we're wrapping up our last day of face shield production, a total of 7,501 face shields. The vast majority have gone to U of M, St. Joe, and Beaumont Hospitals. (Yes, we knew that if we created a punch and die to speed up production, we'd cause the demand to dry up. But that's a good thing. Same idea as bringing an umbrella to keep it from raining.)
Maker Works staff members were led by Irene and included Al, Pamela, Tim, Dulce, KC, Kirstin, and Dale. We also had help from MechShop members Tom and Marty.
A little recognition that has made us feel awesome:
UM article that mentions Maker Works - https://news.engin.umich.edu/2020/04/u-m-approved-face-shield-design-guides-makers-addressing-the-ppe-crisis/
Making it to the Prusa 3D printers website - https://www.prusa3d.com/covid19/#_ga=2.132362766.1015383868.1587895931-525017651.1584621941